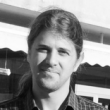
Research Assistant, FESB
Ivo Marinić-Kragić is currently working on his Ph.D in Mechanical Engineering at Faculty of Electrical Engineering, Mechanical Engineering and Naval Architecture, Split, Croatia. To date he has published three scientific papers on generic shape optimization and one conference proceedings on vertical axis wind turbine optimization. Several more scientific papers on the topic of shape optimization are yet to be published. His research interests are Numerical optimization, Coupling of shape optimization and numerical analysis, engineering application of computer fluid dynamics, Parameterizations of 3D shape for numerical optimization, Enhanced reverse re-engineering.
Speeches
Renewable energy sources are expected to gain in popularity in comparison to nonrenewable energy resources that are continually being used up. One of the most researched renewable energy sources is the wind energy, popular since it is renewable, pollution-free, inexhaustible and economically reasonable on both small and large scale. Wind turbines – devices that converts wind energy to electrical power, can be divided in two major design groups. More common group is the horizontal-axis wind turbine (HAWT) used mainly in large scale application. Recently increasing popularity of personal and private renewable energy solutions is followed by the increase in popularity of small Vertical-Axis Wind Turbines (VAWT). VAWTs have some important advantages compared to HAWTs for small scale applications. VAWTs can take wind from any direction without an additional wind direction tracking device, have much lower noise pollution and can convert energy at higher wind speeds. These characteristics are very important for the individual users especially in urban environment application of wind energy technology. A large variety of VAWT designs exist of which most designs can be classified as Darrieus (lift-based) or Savonius (drag–based) designs. They operate at different rotational velocity, measured in non-dimensional number called the tip speed ratio (TSR). Primary advantages of the Savonius designs - lower noise and self-starting are the result of lower TSR but this is also followed by lower energy conversion efficiency. Self-starting ability means that no external motor is required thus simplifying the design. There also exist a variety of solutions which are a mixture between the Darrieus and Savonius designs, trying to combine the advantages of both.
The aim of this paper is to develop a workflow that has an ability to develop a VAWT blade shape for specified both the wind speed distributions and the TSR limits. The developed computational framework enables to synthesize a shape that can be regarded as sort of TSR based compromise between the advantages of both Darrieus and Savonius design, adapted to local wind speed distribution. The shape parameterization is achieved by a B-spline surface based shape parameterization developed specifically for VAWT design. This approach to modeling 3D shapes enables the optimizer to use the same shape parameterization for all designs and a small number of parameters. A reasonable compromise was established regarding reduction of the number of parameters (computational speed) and a loss in shape generality.
The numerical workflow steers the shape of VAWT blades based on the input wind speed distribution and TSR limits. To achieve a reliable workflow, much care is needed in selection and testing of all integrated elements. Efficient geometry parameterization is controlled genetic algorithm based optimizer based on the results from computational fluid dynamics based simulator. This workflow also has to implement the process coupling, passing of data amongst the individual applications including the corresponding data mining. This paper uses computational fluid dynamics (CFD) due to results that compare favorably with experimental data. A good agreement with experimental data in combination with computationally efficient procedure was obtained by full 3D, transient CFD model, implemented in off-the-shelf CFD software. Both local and global optimization cases were conducted with various TSR and the same wind speed distribution. The procedure resulted in different shapes thus allowing a compromise between small TSR and better energy conversion efficiencies.