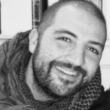
Research Fellow, Politecnico di Bari
Antonio Piccininni was born in Bari, Italy, on 23 November 1982. He received the Master’s Degree in Mechanical Engineering from the Politecnico di Bari (Bari, Italy) in 2012 discussing the thesis “Numerical Investigation of the shifting dynamics of a continuously variable transmission” (academic course: Vehicle Design). In 2012, he joined the Department of Mechanical Engineering, Mathematics and Management (DMMM), Politecnico di Bari, as a winner of a trainee grant in the framework of the PON project “SMATI (Sviluppo Materiali Avanzati e Tecnologie Innovative per turbomacchine per impiego in condizioni estreme)”.
He is currently working at the Politecnico di Bari as research fellow, involved in research activities mainly focused on Finite Element simulations (strain distribution in sheet forming processes and analysis of residual stresses in casting processes) and experimental activities about warm hydroforming, warm deep drawing, residual stress measurements and mechanical/technological characterization of metals at elevated temperatures (light alloys and stainless steel).
He is author of a paper about the numerical investigation for the production of an aluminium bipolar plate via warm hydroforming published on the International Journal of Advanced Manufacturing technology; in addition, he is co-author of papers presented at international conferences about sheet metal forming (Numiform 2013 Shenyang, China; ICC International CAE Conference as speaker Pacengo – Lazise, Italy; MetalFORMING 2014 Palermo, Italy) and creep behavior of stainless steel (ECCC Creep & Fracture Conference 2014 Rome, Italy).
Speeches
Drawability of aluminium alloy is limited by its poor formability at room temperature. The increase of the working temperature is a well-known strategy to overcome such limitation, but, at the same time, a more complex equipment is needed. An interesting alternative solution is represented by tailoring the blank properties prior to the forming process: in such a way, the material strength/ductility can be locally changed by laser in order to improve its drawability at room temperature. In the present work, both the extension of the laser heat treated region and the optimal initial conditions of the base material have been determined coupling the integration platform modeFRONTIER and a 2D numerical model created using the commercial FE code Abaqus. An optimization loop was created in order to (i) avoid the occurrence of fracture during the deep drawing operation (strain conditions as far as possible from the Forming Limit Curve) and (ii) maximize the punch stroke. The maximum Limit Drawing Ratio implementing the heat treated blank was thus predicted.